The restoration of antique wrought ironwork is a specialised craft that blends historical understanding, metallurgical knowledge, and artistic skill. Unlike preservation, which focuses on halting further decay and maintaining the current condition (often reserved for museum-quality pieces), restoration involves repairing or replacing damaged or corroded components to return the ironwork to its former glory. Skilled blacksmiths typically undertake this intricate process with expertise in this unique field. This article delves into wrought iron restoration, exploring the materials, challenges, and techniques professionals employ.
Understanding Wrought Iron: A Historical Perspective
Before embarking on restoration, it’s crucial to understand the nature of the material itself. Historic wrought ironwork primarily falls into two categories:
- Charcoal Iron: Produced until the late 18th century, charcoal iron was created by smelting iron ore in charcoal-fuelled furnaces. The lower temperatures of these furnaces (around 700°C) resulted in a “bloom” – a spongy mass of iron with significant slag inclusions. Repeated heating and hammering removed most of the molten slag, leaving behind a material with around 2% slag content distributed in thin layers or laminae. This characteristic layered structure and a small amount of added carbon (around 0.2%) gave charcoal iron its unique properties.
- Puddled Iron: Invented in 1784 by Henry Cort, puddled iron revolutionised wrought iron production. This process involved “puddling” molten pig iron (produced in hotter coke furnaces) with rods to remove excess carbon. This innovative technique significantly reduced production time and cost, making wrought iron more accessible. However, the quality of puddled iron varied greatly until the introduction of British Standard 51 in 1910, which established quality grades for wrought iron used in railway applications. This standard was later expanded to include general engineering and fencing grades.
Selecting the Right Material for Restoration
Restoring antique wrought ironwork often necessitates the replacement of damaged or missing components. The choice of material for these replacements is crucial and depends on several factors. Options include:
- Salvaged Wrought Iron: Reclaimed wrought iron from architectural or industrial salvage can be a suitable choice, provided its source and provenance are known. The quality of salvaged wrought iron can vary significantly, so understanding its origin is essential. For instance, high-grade iron from redundant ships’ anchor chains can be excellent for re-rolling, while lower-grade iron from fencing or gates might be prone to cracking or splitting during forging.
- Mild Steel: This readily available material gradually replaced wrought iron in the 20th century. While it offers greater strength due to its higher carbon content, mild steel requires more effort to forge than wrought iron or pure iron.
- Pure Iron: Modern pure iron, produced in electric arc furnaces, boasts a high purity (99.8%) and shares similarities with charcoal iron, albeit without the slag inclusions. It is also known as Swedish iron, butter iron, or Armco iron.
- Stainless Steel: This alloy, containing at least 10.5% chromium, is prized for its superior corrosion resistance. It is often used in situations where longevity is paramount. However, it’s crucial to consider galvanic compatibility when using stainless steel with other metals like wrought iron or mild steel, as electrochemical reactions can lead to accelerated corrosion if not adequately protected.
Factors such as durability, cost, corrosion resistance, strength, ease of working, compatibility with adjacent materials, and availability should guide the selection of the most appropriate material. Ultimately, the blacksmith’s skill in shaping and finishing the chosen material will determine the final appearance and quality of the restoration.
Challenges in Wrought Iron Restoration
Restorers of antique wrought ironwork frequently encounter a range of challenges, including:
- Corrosion: While wrought iron’s layered structure contributes to its unique properties, it also makes it susceptible to corrosion. When protective paint coatings fail, moisture penetrates between the iron layers, leading to oxidation and expansion. This expansion can exert significant force, even causing damage to surrounding masonry. Severe corrosion can result in substantial material loss, weakening the ironwork.
- Impact Damage: Often caused by vehicle collisions, impact damage can deform or break wrought iron components. While straightening bent elements might be relatively straightforward, extensive damage or missing parts may require more complex repairs. Old photographs can be invaluable in guiding the restoration process when significant components are lost.
- Previous Repairs: Past repairs, especially those executed poorly, can present further challenges. Unsightly arc-welded repairs or clumsy alterations to adapt a piece to a different location can compromise the ironwork’s integrity and aesthetics. Restorers often need to address these previous interventions before proceeding with their work.
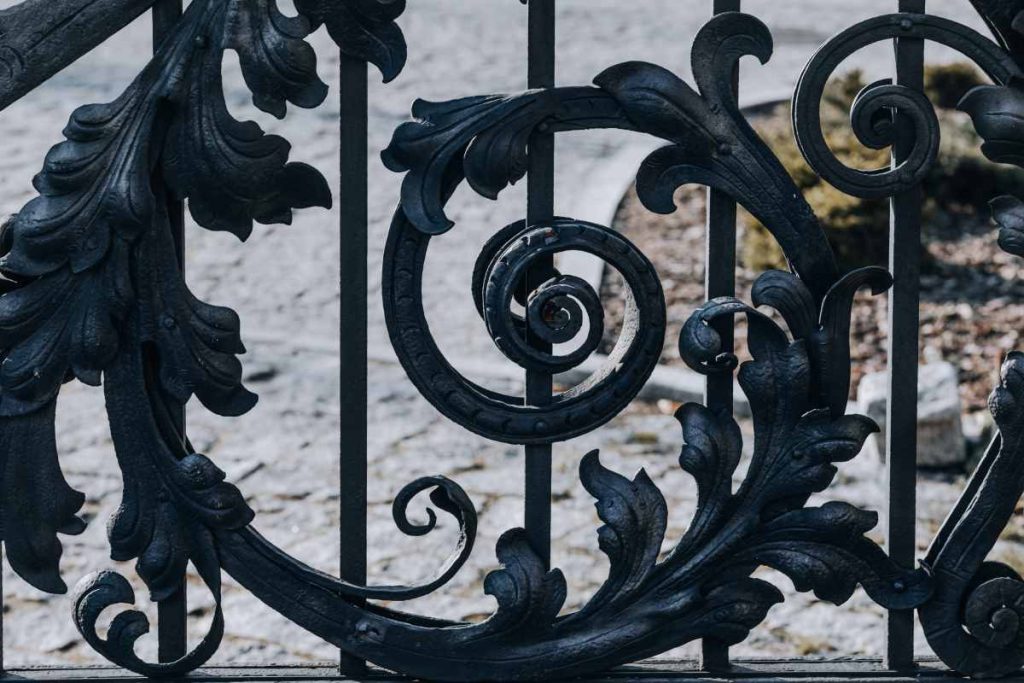
Techniques and Processes in Wrought Iron Restoration
Addressing the challenges mentioned above requires a range of specialised techniques and processes, including:
- Cleaning and Surface Preparation: Before any restoration work can begin, the ironwork must be thoroughly cleaned to remove rust, old paint, and other debris. This often involves a combination of methods, such as:
- Hand cleaning: Using wire brushes, scrapers, and other tools to remove loose rust and paint.
- Abrasive blasting: employing media like sand, grit, or glass beads to remove stubborn corrosion and paint.
- Chemical cleaning: Utilising rust removers or other chemicals to dissolve rust and other contaminants.
- Repairing or Replacing Damaged Components: Depending on the extent of the damage, corroded or broken components may be repaired or replaced. This can involve:
- Forge welding: A traditional technique where heated iron pieces are hammered together to create a solid joint.
- Arc welding: A more modern method using an electric arc to melt and fuse metal.
- Fabrication: Creating new components from scratch to match the original design, often using salvaged wrought iron or mild steel.
- Reassembly and Finishing: The ironwork is carefully reassembled once all repairs and replacements are complete. This may involve:
- Riveting: Joining components together using metal pins.
- Bolting: Fastening components using nuts and bolts.
- Welding: Fusing components using heat.
After reassembly, the ironwork is typically given a protective finish to prevent future corrosion. This may include:
Individual Approaches to Ironwork Restoration
The field of wrought iron restoration is rich with diverse approaches and philosophies. Here are insights from three different practitioners:
- Emphasis on preserving original material using traditional techniques.
- Focus on structural integrity, blending old and new materials.
- Prioritizing historical accuracy and researching original designs.
Frequently Asked Questions about Antique Wrought Ironwork Restoration
- What is the difference between wrought iron and cast iron?
Wrought iron is a malleable and ductile material with a fibrous structure due to its slag inclusions. It was traditionally shaped by hammering. Cast iron, on the other hand, has a higher carbon content, making it brittle and more suitable for moulding into intricate shapes.
- How can I tell if my ironwork is wrought iron or mild steel?
While visual inspection can sometimes provide clues (e.g., looking for the characteristic grain of wrought iron), a spark test can offer more definitive results. When held against a grinding wheel, wrought iron produces fewer sparks than mild steel.
- What is the best way to clean antique wrought ironwork?
The best cleaning method depends on the type and extent of soiling. Gentle hand cleaning with wire brushes may suffice for light rust and dirt. More stubborn corrosion might require abrasive blasting or chemical cleaning. It’s crucial to avoid harsh methods that could damage the ironwork.
- Can rust be removed entirely from wrought iron?
While loose rust and scale can be removed, some pitting or etching may remain on the surface, especially in cases of severe corrosion. The goal is to stabilise the remaining material and prevent further rust formation.
- How much does it cost to restore antique wrought ironwork?
The restoration cost varies widely depending on factors such as the size and complexity of the piece, the extent of damage, the materials used, and the labour involved. It’s advisable to obtain quotes from several qualified restorers.
- How can I protect my restored ironwork from future corrosion?
Regular maintenance is critical to preventing future corrosion. This includes keeping the ironwork clean and promptly touching any damaged paint or coatings. Applying a high-quality protective finish, such as paint, powder coating, or galvanising, can significantly extend the